
A maioria das empresas (fábricas ou indústrias) com processo de fabricação já passou pelos infortúnios do controle de estoque. As vezes faltam materiais, as vezes sobram. Se faltar, a produção para, o mercado não é reposto, o cliente espera mais do que o necessário. E se sobrar, o estoque fica sobrecarregado, e dependendo do material, pode estragar, desatualizar, além de representar um capital parado, imobilizado na empresa. Ainda existem os problemas durante o processo de produção, que por momentos tem suas atividades afetadas e paralisadas, pois um departamento não produziu o suficiente para o departamento seguinte continuar na linha de desenvolvimento do produto. Acontecem acúmulos em determinados setores, e ociosidade em outros.
Em 1953 a Toyota desenvolveu uma solução para esse problema na linha de produção e gerenciamento de estoque. Criou um grande painel, e dividiu-o em três grandes grupos com as cores verde, amarelo e vermelho. Cada cor correspondia a um nível de atenção que os responsáveis de cada setor deveriam ter em relação ao seu estoque. O número de peças prontas era representado por cartões, um para cada peça. Quando uma peça pronta saía do estoque do setor, um cartão era retirado do painel, revelando um sinal verde (que estava por trás do cartão). E assim seguia, peça por peça, cartão por cartão. Até o momento em que, ao retirar um cartão, o sinal revelado seria amarelo. Isso significaria que o estoque estava baixando, e já estava em níveis de atenção. Seria o momento propício de fazer novas cotações de preço, e renovar os itens de estoque.
Enquanto o novo estoque não chegava, as peças ainda estavam em produção, e sendo enviadas a outro setor. E, portanto, os cartões continuavam sendo retirados do quadro, e revelando cada vez mais sinais amarelos. Até que, ao retirar um cartão, revelava-se um sinal vermelho. Isso significaria que o nível de estoque para aquela produção estaria muito baixo, e que deveriam ser tomadas medidas emergenciais para repor os materiais, ou a empresa correria o risco de parar por falta de peça.
Assim que o estoque novo chegasse, os materiais seriam repostos, e os cartões voltariam para o painel. É importante salientar que o novo estoque comprado é no mesmo número de cartões que foram retirados do painel, justamente para evitar desperdício e acúmulo de estoque.
O PROCESSO
Esse processo ficou conhecido como KANBAN, que na tradução significa “cartão visual”. Atualmente é utilizado em linhas de produção como montadoras de veículos. A técnica foi aperfeiçoada, adicionando mais cores, em mais etapas. Porém, a essência do mecanismo continua o mesmo: evitar desperdício e ociosidade, mantendo a linha de produção harmoniosa e com ritmo.
Para uma empresa, o Kanban pode facilitar os procedimentos internos, pois permitiria visualmente entender como e de onde vem o fluxo do processo, e seu destino. Funciona melhor ainda se utilizado em concordância com outras técnicas, com o fluxo SIPOC, que também analisa processos internos, porém nomeando as entradas e destinos de informações. O Kanban dá suporte ao just-in-time, que utiliza a ideia de não produzir enquanto não houver demanda, portanto previne os colapsos entre os setores. Essa eficiência na produção auxilia no fluxo do processo como um todo, fazendo a empresa não parar, não ser rápida demais, nem muito lenta.
Inicialmente o Kanban era muito utilizado nas indústrias de produção e empresas de logística, mas atualmente, fazendo as adaptações necessárias, qualquer empresa pode utilizar. Atualmente é amplamente utilizando em empresas de softwares, agências de publicidade e até mesmo por prestadores de serviço, pois é um método totalmente moldável ao tipo de negócio praticado. Deve-se ter o cuidado de aplicar a técnica com o objetivo correto, que é eliminar desperdícios e ociosidades, refletindo em uma melhor administração financeira dos recursos.
Se sua empresa tem procedimentos, setores e responsáveis, é bom pensar no Kanban para ajudar a visualizar o processo na sua homogeneidade. Com certeza serão detectados os gaps, as falhas de comunicação, os acúmulos de atividades ou materiais, e ao final da aplicação das melhorias, certamente o resultado será um melhor fluxo das informações, além de possivelmente a economia financeira. E lembre-se: o Kanban serve pra todos. Basta adaptá-lo ao tamanho do seu negócio.
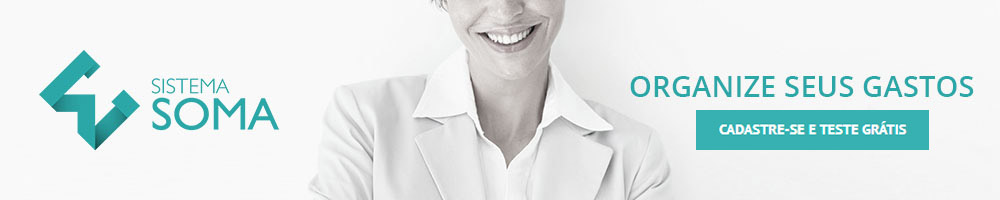
Gostou de nossa matéria? Não se esqueça de compartilhar nas redes sociais e de se inscrever em nossa Newsletter para receber mais matérias como esta e também conteúdos gratuitos sobre empreendedorismo, finanças e marketing. Em caso de dúvidas, críticas ou sugestões, deixe seu comentário logo abaixo.
Participe e Comente